As interconnect speeds exceed 10Gbps, engineers and designers are struggling to solve how to maintain signal integrity while maintaining a reasonable thermal management budget. Due to the excessive heat dissipated by the system, how to keep the system below a reasonable level to prevent premature failure or personal injury (temperature of the connector) is a challenge for engineers and designers. In this article, we will discuss how to reduce interconnect power consumption and various technologies for thermal energy management in today's high-speed world.
Service providers are rapidly expanding their capacity, and the transmission and transmission bandwidth required for this purpose—the way that 10G is interconnected via Ethernet switches and servers is very common. As the data transmission rate exceeds 10Gbps, it is becoming more and more difficult to maintain signal integrity and manage the increasing power demand. For faster speed, more power is needed. To achieve faster speeds at the same distance, active circuits or special materials are required. So, is there a solution suitable for this conversion and upgrade?
Optical interconnects and alternatives
In many high-speed data applications, there is an ASIC or FPGA that is completing or is processing the exchange. Examples include switches that make up the connection structure and firewalls that use deep packet inspection technology, where throughput is the key to the design. These types of system interconnections are usually through fiber optic modules located near the back of the device that connect fiber optic cables. Until recently, most ASICs or FPGAs could not directly provide the built-in 10G Ethernet connection, so a physical layer device (PHY) used slower data (XAUI) that aggregates multiple channels to achieve the 10G Ethernet standard. This allows designers to transfer slower data on their printed circuit boards (PCBs) and less likely to encounter some signal integrity (SI) issues (see Figure 1).
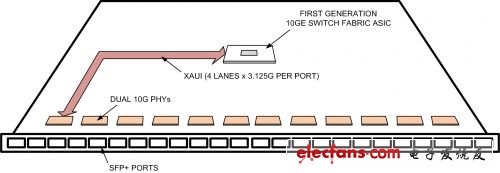
However, with the recent introduction of 32nm (and smaller) CMOS processes, 10GE devices have been able to be integrated into a central ASIC or FPGA. In most applications, this is a significant advancement, because system engineers can achieve higher density in their device designs-this is indeed the case (see Figure 2). However, this poses a new problem because the integrity of the 10G signal will deteriorate rapidly before reaching the fiber optic module connector. The low-voltage CMOS with smaller emission amplitude limits the output level of the signal. In addition, if these modules are far from ASIC or FPGA, it may be difficult to meet the very strict input jitter requirements. To solve this problem, a signal conditioner device can be placed near the connector to help reduce jitter to meet specifications. In many cases, with the increase of high-density switches, the additional power consumption will cause the temperature of the air to rise, and the air is used to cool the optical fiber module inserted into the back of the system. To reduce power consumption. National Semiconductor ’s single-channel DS100BR111 and four-channel DS100BR410 are good examples of this requirement. Both components are 10G buffer repeaters with very low power consumption. Increasing the power consumption near the connector may cause problems with the temperature of the fiber module, so keeping power consumption low is critical.
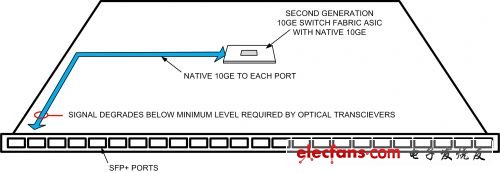
In addition, the system is also beginning to use active copper cables to replace optical module interconnections less than 15 meters in length. This trend mainly comes from users hoping to reduce the cost of interconnection, and the optional use of fiber optic cables at shorter transmission distances. Active copper cables basically use the same technology as described above. In addition to the buffer repeater device inside the connector housing, equalization and de-emphasis are also used to compensate for cable losses. However, due to the high-density connectors on the back of these systems and the limited airflow or high air temperature, building an active cable still requires very low power consumption. In fact, if the power of the active components is not low enough, the temperature of the connector housing may rise enough to cause serious burns to the technicians who move the cables.
Several manufacturers such as Molex, Tyco, Amphenol, and others have also begun to integrate heat sinks in fiber optic module cages to help eliminate residual heat. This helps to manage the thermal footprint of the module to ensure normal operation. However, for some installation customers who use passive cables in order to shorten the running distance, a larger diameter wire assembly is required. When these cables are plugged into the back of a rack in large quantities, they may actually obstruct airflow and cause the operating temperature of the equipment to rise. This is another reason for users to switch to active copper 28 or 30 AWG wire. Compared with the bending radius of passive wire components and similar optical fibers, the latter has a smaller diameter.
The future is no longer so far away
As the demand for bandwidth continues to increase, operators and service providers will need higher capacity and higher density interconnects. At present, most enterprise switches and server interfaces are 10G Ethernet, and the information architecture that has been deployed in place can support optical fibers and copper cables-whether active or passive. 40G Ethernet uses four channels of 10G, while 100G uses ten channels. However, the next step will be to migrate to 25G interconnect, which will simplify the WDM fiber module used to transmit 100G Ethernet. Due to the need to operate at a faster speed and the need to increase the interconnect density, which leads to an increase in power, it is expected that a series of new heat dissipation problems will occur around 2012 or 2013.
The need to increase airflow to improve the cooling capacity of the system creates problems associated with mechanical fans. However, NuvenTIx's new cooling technology uses the so-called "entrainment" phenomenon, which can help keep the airflow around the connector without rotating the fan. These coolers generate jets of air and pull the surrounding air into the cooler, which has a life span of 100,000 hours. These coolers have been used in LED cooling systems that have high service life requirements and care about the effects of excessive noise caused by the use of rotating fans.
in conclusion
As our desire to share rich media (Rich Media), streaming video and real-time downloads increases, so will the demand for bandwidth. Faster systems require more power, and new methods are needed to use power more efficiently, or to deal with related heat dissipation. An optimal solution is to transmit data faster at lower power levels. Perhaps sometime in the near future, people will find an all-fiber network solution. Copper cable still has a very long life, and some solutions today have made digital signals far beyond 25Gbps.
Neon Light Letters,Custom Led Signs Indoor,Neon Light Signs For Bedroom,Neon Light Board
Tes Lighting Co,.Ltd. , https://www.neonflexlight.com