In the medical electronic equipment industry, home health care is the fastest growing field. Driven by the prolonged life expectancy of human beings, the increasing number of chronically ill patients and the increasing cost of healthcare, more and more “smart†and “friendly†medical devices are entering the home consumer market.
These healthcare products include: blood glucose meters, digital sphygmomanometers, blood gas analyzers, digital pulse and heart rate monitors, digital thermometers, pregnancy testers, transdermal drug delivery systems, dialysis systems, and oxygen concentrators. Many of these instruments can be wirelessly connected to the office of the medical staff through the Internet to achieve continuous online monitoring and diagnosis of critical patients.
As the technology used in medical electronic products is becoming more and more complex, in order to ensure that everyone including medical personnel, patients themselves and the most important home users can use these products safely and effectively, the design requirements for these products are becoming more and more High, and many of these requirements may conflict. For designers, all this means realizing more functions on a chip or circuit board in a given space while reducing power as low as possible.
"When choosing an IC for home health electronics, the biggest problem facing designers is how to balance various aspects reasonably, such as small size, low power, low cost, high reliability, long life and high safety. "Steve Kennelly, senior manager of Microchip ’s Medical Electronics Division, explained," How much processing power is required depends on who is the user of the medical electronic device. "
The production volume of many medical electronic devices is not very large, so it is difficult to achieve lower market costs through automated manufacturing processes. Of course, a positive sign is that the prices of individual electronic devices (sensors, MCUs, displays, memories, etc.) in these products are falling.
Another obstacle faced by medical electronic equipment is how to achieve tightness much higher than that required by non-medical electronic equipment, and the overall miniaturization makes the tightness more difficult to achieve.
Understand the requirements of home medical electronic equipment
For doctors and other professionals to operate medical electronic equipment is handy, because they have trained the use of these instruments. For family patients, simple operation is extremely important. Fortunately, the latest highly integrated chips, sophisticated DSPs and microcontrollers, high-density flash memory, and advanced micro-electromechanical system (MEMS) sensors all contribute to this goal.
"We welcome these seemingly contradictory requirements because they provide us with opportunities for innovation." Todd Schneider, vice president of the medical business unit of AMI Semiconductor, said that many of the company's medical electronic designs use ASSP And Application Specific Integrated Circuits (ASICs), "We have been in the medical electronics industry for more than 20 years, so we understand the technical challenges these devices face."
Depending on the specific practical application, the performance priority setting of each healthcare electronic product will be different. For example, for products such as portable blood glucose meters (often using disposable chemical test strips), low cost is the highest priority parameter. The portable home dialysis system must make reliability and long life as the top priority in the design, and the cost is second. Implantable devices such as pacemakers must have high reliability, small size and long life, and power consumption should be as small as possible. Cost is not a major consideration in this case.
Size is very important
Because people put forward many performance requirements for medical electronic products, engineers have to face various design trade-offs. This means that they need to weigh carefully when deciding what type of sensors, analog-to-digital converters, amplification and filtering, control and data processing, power supplies, displays, and wireless transceiver circuits.
Size is usually the main design constraint, especially for medical implantable electronic products, minimal tissue penetration is absolutely necessary. Such implant products generally include a sensor, some signal processing circuits or a transmitter. All these devices need to be inserted into a miniature catheter or probe and then inserted into human tissue. The small size also makes it easier for doctors or medical personnel to place implanted products into a person's body.
For example, some smart pills containing sensors, cameras, and RF transmitters can be used to clearly and non-invasively observe the internal organs of the body. DexCon's implantable blood glucose monitor uses the ultra-low power ASIC system-on-chip provided by AMI Semiconductor. It continuously monitors the condition of diabetic patients through the RF transmission function in the 402-405MHz frequency range.
Disposable blood glucose meters will also become smaller and smaller, and the current typical size is as large as a handheld personal digital assistant (PDA). Some blood glucose meters are even as big as small watches, but they still contain sensors, microcontrollers, liquid crystal displays (LCDs) and batteries. These instruments usually use optical or electrochemical sensors to measure blood glucose values. The patient only needs to pierce his finger to drop a drop of blood on the disposable test strip, and the blood glucose meter can read the blood glucose value. One-time use of machines and test strips must also be designed for low cost.
The wireless electrocardiogram (ECG) Holter monitor is a good example of miniaturization. The monitor designed using ADI's existing IC is very small and can be installed on the back of the ECG electrode. With lower noise and greatly reduced interference signals, this monitor can provide a more accurate signal than traditional designs.
Reduce power consumption
Lower power consumption is the dream goal of medical products, especially battery-powered and portable household equipment. In simple terms, reduced power means longer battery life. It also allows designers to flexibly use smaller batteries and give full play to the advantages of the latest MCU chips with power management performance.
However, low power consumption is not always associated with smaller battery sizes. When computing power is required, like a cochlear implantable hearing device, the battery may be larger than the circuit. Cochlear implantable devices must work in dynamic mode, and static 'sleep' mode is difficult to use. The power supply for these implanted products generally comes from an inductive power supply worn outside the ear. These products must use a fast clock rate and operate continuously with a wide dynamic range, so they consume a lot of power.
Another issue affecting power consumption is the IC manufacturing process. ICs manufactured with a 0.13 μm process have greater leakage current and static power consumption than previous generation ICs manufactured with a wider wire diameter. "We reduce the power consumption by optimizing the chemical composition of IC wafers during the manufacturing process," said Todd Schneider of AMI Semiconductor.
Reducing the operating voltage of the IC and carefully managing the capacitance effect are of great help in reducing leakage current. This is why medical electronics system manufacturers use (in three-dimensional packaging) chip stacking instead of squeezing each device to occupy board area on a plane of limited size.
Fortunately, some specific technologies help manage power consumption. For example, reducing the clock rate and shortening the operating time in dynamic mode can be used to reduce power consumption. "The key is to quickly power on." Schneider pointed out. Wake up the chip to quickly enter dynamic mode and put it in sleep mode as long as possible to ensure lower power consumption.
A deep understanding of the specific application's demand for IC functions is of great value, and it can help designers implement all necessary functions in hardware with gates. Although this method is not very flexible, it does significantly reduce any unnecessary functions on the chip, thereby effectively reducing power consumption.
TI recently introduced an ultra-low power MCU with a complete signal chain that can be used in various portable medical diagnostic equipment, such as personal blood pressure monitors, spirometers, pulse oximeters, and heart rate monitors (Figure 1). This 16-bit reduced instruction set processor (RISC) SoC, model MSP430FG4270, integrates a comprehensive functional chain that can help designers develop low-cost portable medical devices.
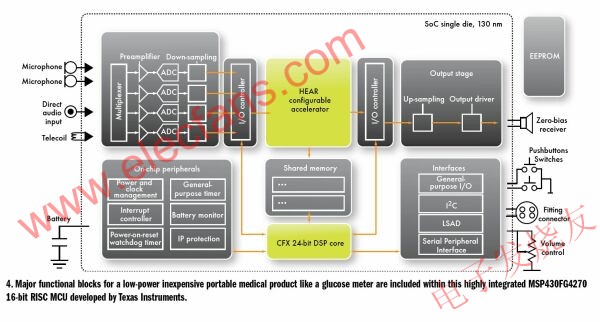
Figure 1: The highly integrated MSP430FG4270 16-bit RISC MCU developed by TI integrates the main functional modules required for low-power, low-cost portable medical products (such as blood glucose meters).
There are 5 low power modes that can be used to extend battery life. In standby mode, the power consumption is only 1.1μA, and the operating voltage is 1.8 to 3.6V. At 1MHz and 2.2V, the power consumption of the device is particularly low, only about 250μA. The unit price for a 10,000-piece order is $ 3.78, which is the lowest among similar chips in the industry, according to TI.
NEC Microelectronics has also introduced inexpensive 8-bit MCUs, such as the 78k0 / Lx3 series, many of which are specifically designed for portable healthcare electronic applications. This all-flash device integrates an on-chip LCD controller / driver, consumes very little power, and consumes only 2.3μA in standby mode.
The industry has also made significant progress in developing very high-quality sound for ultra-low power hearing applications such as hearing aids. AMI Semiconductor ’s Ezairo 5910 ASSP integrates a flexible filter engine called a hearing enhancer, which can provide very high-quality sound at extremely low power. This hearing enhancer consumes less than 1mA and can provide the full 24-bit processing and long battery life required for high-quality sound.
DSP enters home medical electronics
DSP is also more and more widely used in medical electronic products, it helps to deal with complex operations and reduce power consumption. They have a great role in portable medical ultrasound imaging equipment and can be used to achieve more accurate and clearer 3D imaging quality than previous 2D products.
In the core part of an award-winning sub-band electronic stethoscope designed by ATM Semiconductor, it is equipped with an ultra-low power DSP, which uses signal processing technology using an oversampling filter bank. This DSP provides 21dB of amplification performance, which greatly improves the performance compared to traditional stethoscopes that attenuate sound signals. The device operates at 1.8V and consumes only 4.1mW of power. The power consumption of the entire electronic stethoscope is 47mW, and most of the power consumption (43mW) is consumed by the LCD reading device.
Table Top Cooker,Three Burner Gas Cooker,Ce Tempered Glass Gas Cookers,3 Burner Gas Stove With Ce
Xunda Science & Technology Group Co.ltd , https://www.xundatec.com